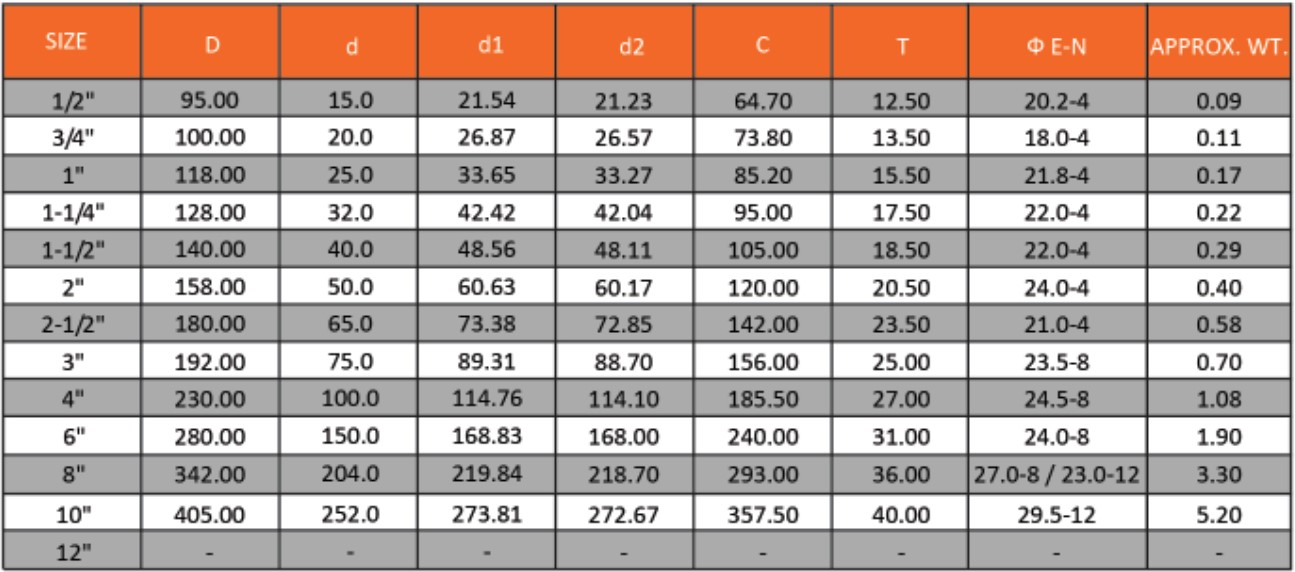
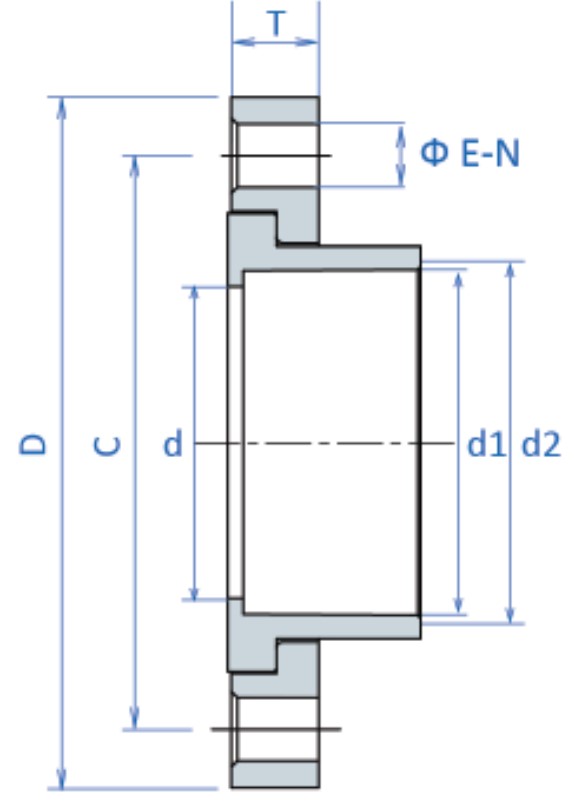
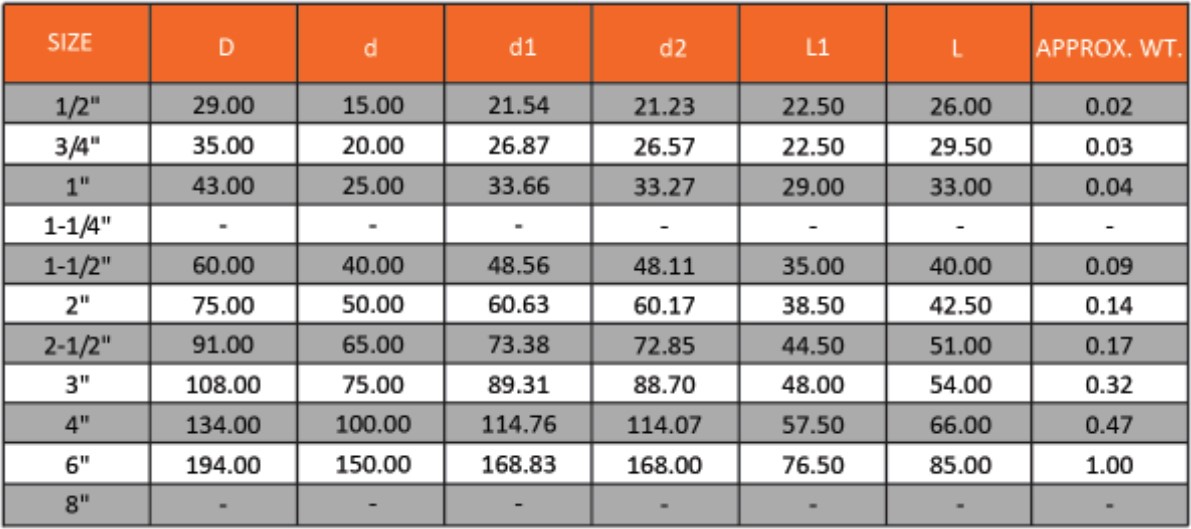
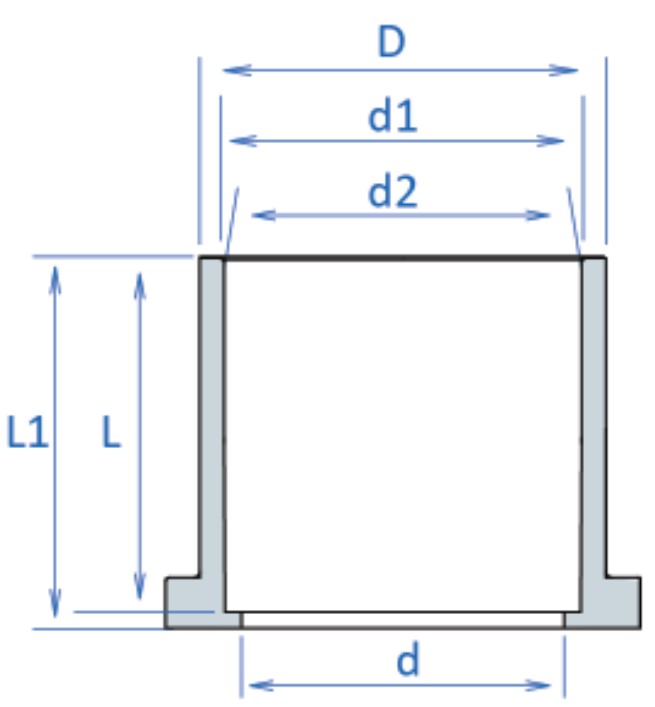
Flanged PVC & CPVC tube has an advantage when used in a system where there is a need to dismantle the tube occasionally or when the system is temporary and mobility is required. Flanging can also be used when it is environmentally impossible to make solvent-cemented joints on location.
A. Selection of Materials:
Gasket – full-faced elastomeric, ( Durometer “A” scale of 55 to 80, usually 1/8″ thick). Must be resistant to chemicals flowing through the line.
Fasteners – bolts, nuts, and washers, also resistant to the chemical environment. (Threads should be well lubricated).
Torque Wrench – a necessity for tightening bolts in a manner that guards against excessive torque.
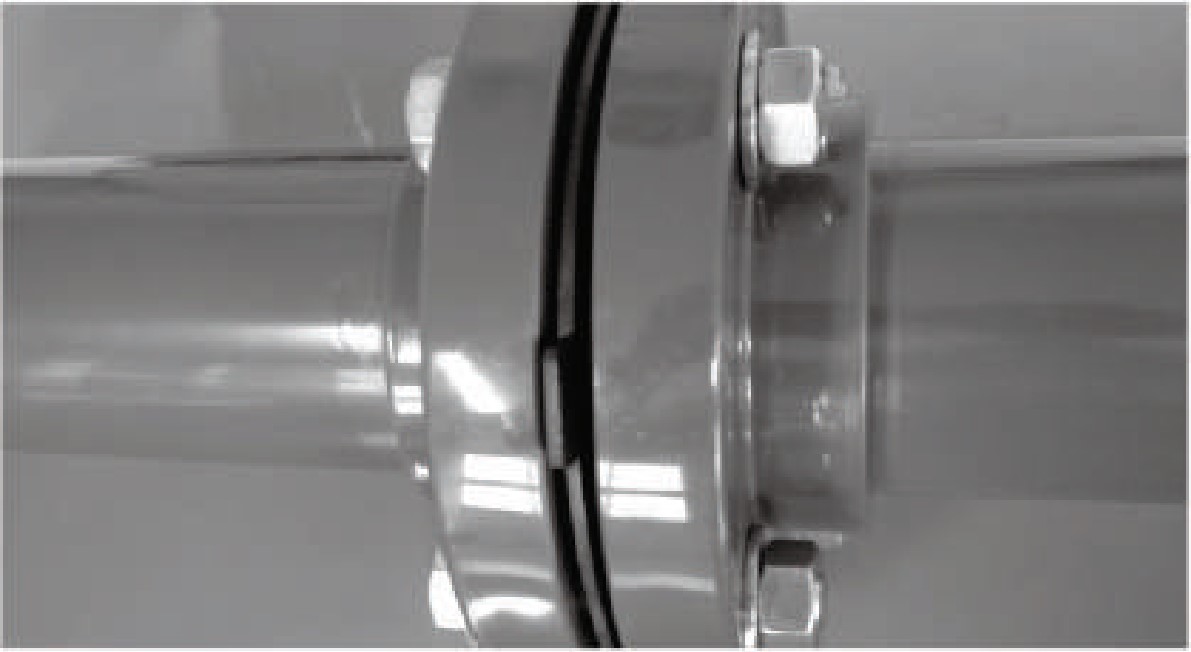
B. Flange Assembly:
Join the flange to the tube as outlined in the solvent cementing section or in the threading section depending on the joining method desired.
Align the flanges and gasket by inserting all of the bolts through the matching bolt holes. Proper mating of flanges and gaskets is very important for a positive seal.
Using a torque wrench, tighten each bolt in a gradual sequence as outlined by the flange sketch. For the final tightening of all bolts, find the recommended torque value in the chart below.
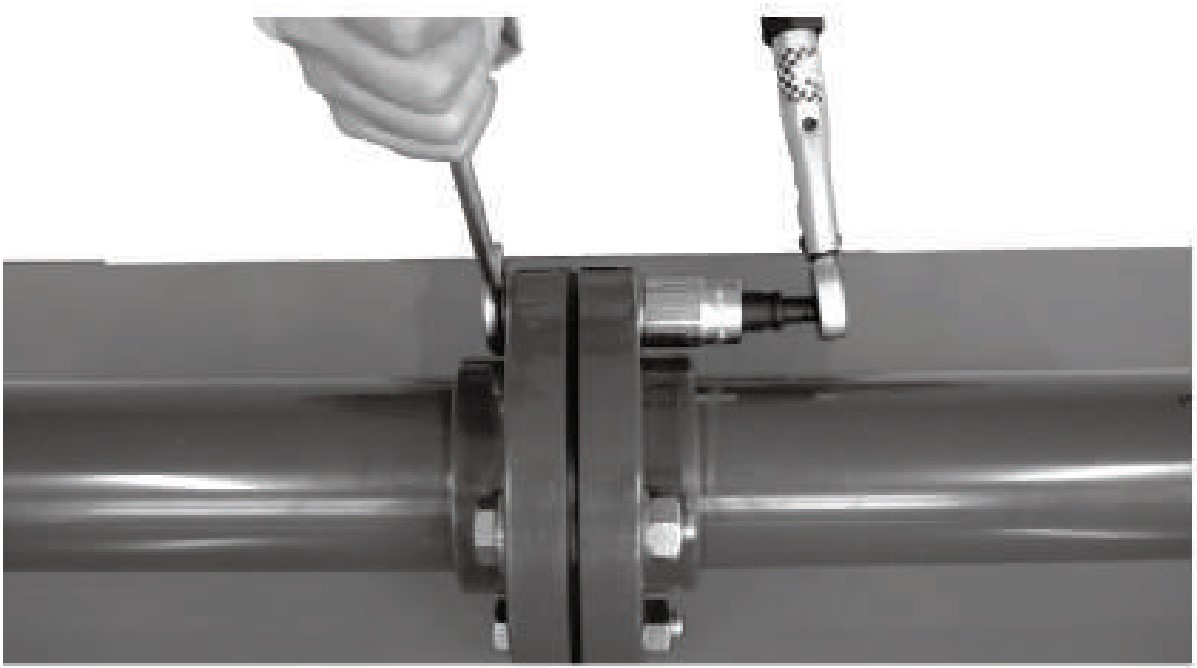
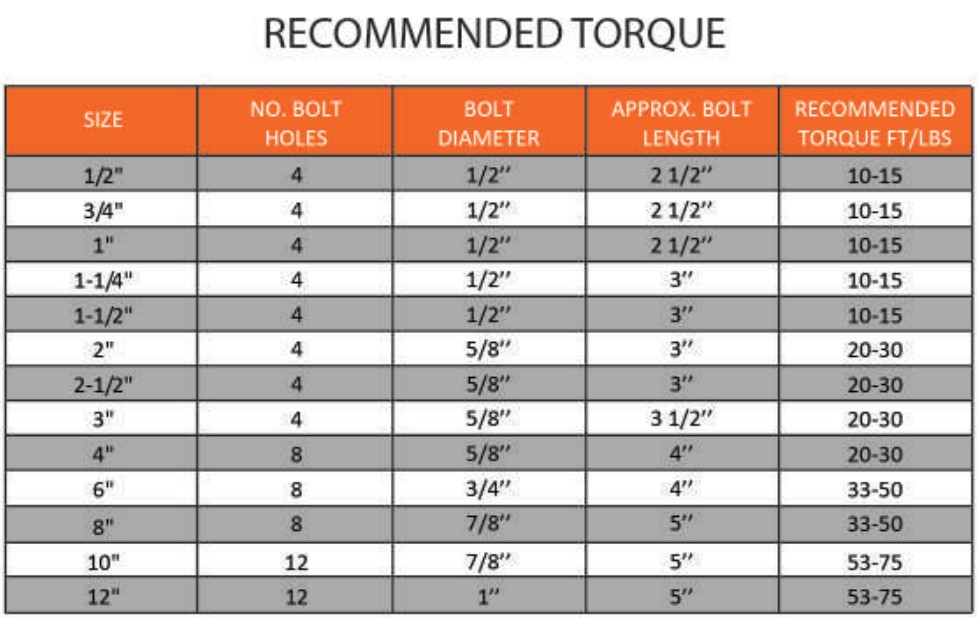
Cautions:
1. Do not over-torque flange bolts.
2. Use the proper bolt tightening sequence.
3. Make sure the system is in proper alignment.
4. Flanges should not be used to “cold-spring” the system. 5. Flat washers must be used under every nut and bolt head.